- kingda XPS - flame retardant board
- kingda xps - The common blue, red, yellow
- kingda xps - Roof extrusion board
- kingda xps - Internal and external wall extrusion
- kingda xps - Cold storage and purification worksho
- kingda xps - Floor heating extrusion board
- kingda xps- Steel structure layer and sandwich ext
- kingda xps - Special shape sheet extrusion board
- Promotion Keywords
Dongguan city, kingda plastic insulation board co., LTD
Contact: manager zhao
Mobile phone: 13509011897
The phone: 0769-88127882
Fax:0769-88128231
Email:2875488916@qq.com
Web site:www.dgkingda.com
Address:Zhongtang town Zhancui Nan di Industrial area
-
Construction preparation
1. Material preparation
1.1 the acceptance, storage and transportation of materials shall comply with the relevant requirements and be classified and listed. Extruded board package including polymer mortar and special binder; storage should pay attention to rain moistureproof; steel wire mesh, fixed parts should also be stored rain..
1.2 insulation mortar composite materials should avoid dampness and rain during transportation and storage.
2. Construction tools
Electric wire cutter, electric mixer, wallpaper knife, electric screwdriver, scissors, a hacksaw blade, ink and brush or roller, sand paper, plastic mixing barrel, impact drill, hammer, trowel, pressure, yin and yang angle, supporting board, 2m Minzi ruler etc.
construction technology
1, process flow
2, construction process
2.1, grassroots treatment
2.1.1 has clear influence acceptance of primary wall paint, oil, dust, hollowing and weathering materials such as bond strength.
2.1.2 for engineering exterior wall, check with 2m foot, the maximum deviation should be less than 4mm, exceed the difference should be picked or cut with 1:3 cement mortar repair leveling.
2.1.3 in order to increase the adhesion between the Extrusion board and the base, the interface agent shall be painted on the surface of the extruded board, and then the polymer mortar shall be used as an adhesive or protective layer.
2.2, bomb control line
According to the building facade design and external wall insulation technology requirements, on the grassroots level, vertical lines, vertical control lines.
2.3. Hang the datum line
2.3.1 hang out vertical baseline control lines and level control baselines on the outer walls, corners (corners, horns) and other necessary locations.
In the course of 2.3.2 construction, each layer should be properly hung horizontally to control the verticality and integrity of the extruded board.
2.4. Prepare special adhesive
2.4.1, use a clean plastic mixing barrel into five parts of dry mixed mortar, add a water, attention should by adding water and stirring, and then use the hand-held electric mixer stirring for about five minutes, stirring until evenly, and medium consistency so far. Ensure that the polymer mortar has a certain viscosity.
After the completion of 2.4.2 and above work, the mortar should be laid aside for 5 minutes, and then stir it can be used. The mortar should be finished in an hour.
2.5, paste, flip bag, mesh cloth
2.5.1, where the extrusion panels are exposed at the side, the door and window openings should be done with grid cloth.
2.6. Stick the extrusion plate
2.6.1, standard outer wall extruded board size is 1200 * 600mm. Non standard size and local irregular place can be cut by electric hot wire cutter or tool knife, the dimension tolerance is + 1.5mm, the size is vertical. Extruded panels with a minimum size of more than 300 mm are applied to the corners of the entire wall.
2.6.2, in the Extrusion board surface (single-sided) thin batch of scraping a special interface agent, to cool dry, you can daub special adhesive.
2.6.3, using a method paste extruded board: trowel on each extruded board has brushed interface agent side peripheral smear width of 50 mm from the edge to the center gradually thickening of special polymer mortar, and its thickness is 10mm, then put 9 points in extruded board layout plum, plum point spacing uniform size sure, extruded plate bonding area was more than or equal to 30.
2.6.4, painted gray immediately after the Extrusion board affixed to the wall, and 2M by the foot of its extrusion leveling, to ensure its vertical, smoothness and bonding area meet the requirements. No adhesive mortar shall be applied at the meeting place, and a mortar shall be removed in time. Between the board and the board to squeeze tight, no seam, seam exceeds 1.5mm extruded sheet packing. The seam height is less than 1.5mm, otherwise the application of polishing grinder.
2.6.5, when construction, the Extrusion board should be horizontal paste, the upper and lower two row of extrusion plate should be vertical stagger each other, 1/2 board length, to ensure that the minimum wrong joint size is not less than 200mm.
2.6.6, at the corner of the wall, you should first size, cut the extrusion plate, so that the vertical connection of the paste to ensure that the corner straight and vertical.
2.6.7, when pasting the positive angle around the window frame and the positive angle of the outer wall, the reference line should be ejected as the basis for controlling the vertical and vertical angles of the positive angle.
2.7 、 install fixing parts
2.7.1, to be extruded board firmly affixed, generally installed within 24 hours fixed parts, according to the design requirements of the location of drilling with impact drilling, the anchor depth of 50mm, drilling depth of 60mm.
2.7.2, number of position fixing pieces:
Five to seventeen (including seventeen) per square meter is about 6;
Any single plate with an area of more than 0.1 square meters shall be secured with a fixed quantity depending on the shape and the conditions of the field.
2.7.3, a fixed encryption: yang angle, under the eaves, windows and doors around encryption, from the base edge is not less than 60mm, the spacing is not greater than 300 mm.
2.7.4, self tapping screws should be tightened, and engineering plastic expansion nail hat and Extrusion board surface uniform or slightly twisted into some, to ensure expansion screw tail back, so as to make it fully anchored with the base.
2.9, grinding leveling
2.9.1, after the construction of the fixed parts, apply rough sand paper to the uneven joints of the extruded board, and the grinding action shall be gentle and smooth, not along the equal direction with the extrusion plate joint.
2.9.2, after grinding the grinding operation application brush debris and other dust clean
2.9.3, on the Extrusion board paste uneven place, the use of surface layer of polymer mortar leveling. Brush the interface agent before leveling.
2.10. Apply polymer mortar base course
A thin interface agent is applied on the surface of the extruded board. After drying, the polymer mortar is evenly applied to the extrusion plate, and the thickness is about 2mm.
2.11 press in the mesh cloth
2.11.1 and apply the polymer mortar immediately after pressing into the mesh cloth.
2.11.2 and mesh fabric shall be cut according to the length of the work face and shall be provided with lap length.
2.11.3, door and window opening and the periphery of the inner side walls form 45 316LVM yang angle of each with a layer of 300mm * 200mm mesh were strengthened, large surface mesh lapped on the door and window openings around the mesh cloth.
2.11.4, for the window, door and other openings around the end of the Extrusion board, the use of mesh cloth and bonded mortar to wrap it, and only at this time to allow the extrusion plate coated with bonded mortar.
2.11.5, the large surface mesh along the horizontal direction stretch straight flat, and a curved face, with a trowel from the middle to upper and lower sides of the mesh is smooth, so close to the bottom of the polymer mortar. The grid cloth left and right lap width not less than 100mm, and the lap width not less than 80mm, the local joint available polymer mortar added the original polymer mortar deficiencies, and shall not make mesh folds, hollowing, alice.
2.11.6, in the Yin and Yang corner, but also from each side of the two-way angle, and lap each other, the width is not less than 200mm.
2.12, surface layer of polymer mortar
Wipe the bottom of polymer mortar, mortar dry and not sticky to be pressed into the mesh, surface layer of polymer mortar, plastering thickness to cover the grid for the standard, about 1mm. The total thickness of mortar protection layer is about 2.5 + mm0.5.
Construction of thermal insulation mortar
Main performance index of thermal insulation mortar
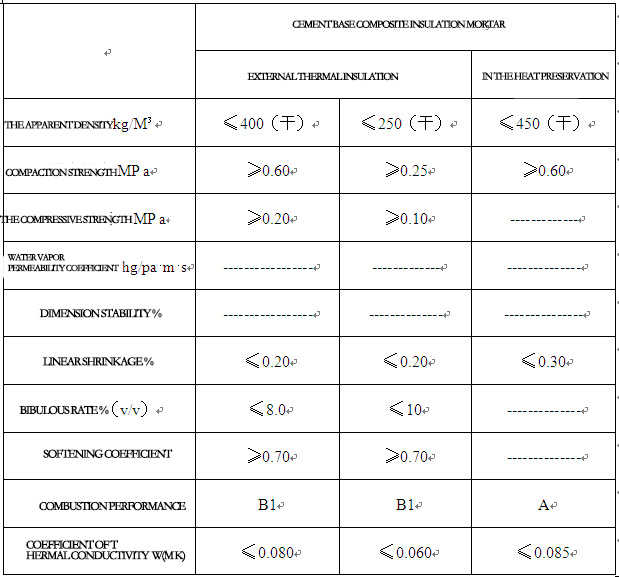
1, process flow
The 1.1 basic processing, set square and find rules do wipe 15 thick ash cake, insulation mortar, steel wire, electric hammer drill hole, covered with 8mm thick mortar and acceptance, water conservation.
1.2, grass-roots treatment: with Extrusion insulation board exterior wall approach.
1.3, find the rules do ash cake: ash cake practice with extruded insulation board wall, ash cake thickness 15mm, with thermal insulation mortar, Yang corner are corner protector for 1:3 cement mortar, and then wipe the insulation mortar.
1.4, apply insulation mortar
1.4.1 composite insulation mortar mixing stone should be considered when environment temperature and humidity level determine the ash water weight ratio, the ratio of material to water for general powder: Powder: water =1:0.65, viscosity should be controlled in the range of 60-80mm, with the mix with the use, the general should be finished within 4 hours;
1.4.2 determine the thickness of the construction, the insulation mortar composite material should be layered coating, each layer thickness is not greater than 12mm.
1.4.3 thermal insulation layer, the thermal insulation mortar shall wipe again to apply (Note: the operation of workers to the wrist force, to reach the final setting material), (about 24 hours) with second times (according to the insulation mortar again wiping method). Second times to reach seven layers of insulation mortar dry, with a trowel compaction rub hair, shave with his feet by standard block, uneven fill insulation mortar until now can be flat, surface finishing;
1.4.4 heat preservation layer after finishing, watering and wetting. Keep the surface white, water maintenance time shall not be less than 7 hours.
1.5, laying and installation of steel wire mesh, supporting insulation nails
Main performance index of reinforcement network
The insulation layer is finally coagulated (about 3-4 days), according to a certain distance with the hammer drilling (4 /m2, the depth of the hole is greater than the length of about 10mm insulation nail); wire mesh in the insulation layer on (Note: facing the bending wire, the joints should take about 50mm-80mm) according to the original pitch; install the expansion nail and fixed with steel wire net.
1.6 、 crack prevention mortar construction
Adhesives - interface mortar and anti cracking mortar main performance indicators
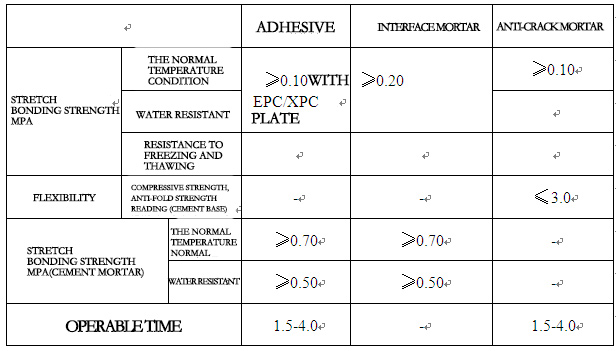
1.6.1 anti crack mortar layer construction preparation: anti crack mortar layer plastering insulation layer must be carried out in a fully solidified after 5 days, the day before the construction of water. Water the water again an hour before plastering.
1.6.2 mortar cracking should be mixed with use, parking time should not exceed 2 hours, not landing ash recycling; crack mortar: anti crack waterproof agent: Sand: water =1:3:0.75 (weight ratio), consistency control in 60mm ~ 90mm.
1.6.3 thickness design requirements of impervious and anti crack surface layer is about 8mm (Note: according to the smoothness of insulation layer)
1.7, acceptance, watering and maintenance
Anti cracking mortar layer according to the seasonal temperature well maintenance, material initial setting after water conservation, water conservation is not less than 7 hours, watering maintenance intervals of not less than 7 hours;
Five, quality inspection methods and key points
1. Guarantee project
1.1. The specifications and technical specifications of Extruded Boards, composite thermal insulation mortar, mesh cloth, the preparation of polymer mortar and the quality of raw materials must comply with the requirements of these procedures and standards. Inspection method: check the factory certificate or retest.
1.2. The polymer mortar and the Extrusion board must be bonded tightly without delamination. Methods of examination: observation and hand push and pull examination. Observation. Check the quantity: check two floors every three floors.
1.3, the polymer mortar and extruded board, thermal insulation mortar and base must stick tightly, no delamination, hollowing. No blasting ash and cracks on the surface.
Test method: with a small hammer to tap and observation checks
Check the quantity: check two floors every three floors.
1.4 、 sampling and re examination of tensile strength of anchor bolt. Design requirements, according to the design requirements of the number of testing, design requirements shall not be less than 1 per thousand, and no less than 3 (for thin plastering exterior insulation system, the number of testing each building is not less than 1 groups).
1.5, exterior wall tile bonding strength testing. Site mounted exterior wall tile project, each 500m2 similar walls take a group of specimens, each group of 3, every two floors may not be less than 1 groups; less than 500m2 of similar walls to draw a group.
2, basic project
Each piece of extruded plate and grassroots surface bonding area of about more than 30%.
Method of examination: ruler scale examination takes its average value.
Check number: according to floor every two checks a check every layer, not less than 2.
Note: the test shall be done prior to the coagulation of the binder.
The expansion plug part of the engineering plastic fixing component shall be no less than 50mm of the structural wall.
Test method: withdraw self tapping screw, observe and check.
Check number: according to floor every two checks a check every layer, not less than 2.
The Extrusion board shall not be coated with adhesive.
Method of examination: observation and examination.
Check number: according to floor every two checks a check every layer, not less than 2.
Mesh should be horizontal laying, pressing compacting, not wrinkle, warping, exposure phenomenon, lap width not less than 100mm or less than 80mm, not on.
Method of examination: observation and ruler examination.
Check number: according to floor every three checks a check every layer, not less than 2.
Before applying special adhesive and polymer mortar, check whether the interface agent has been brushed (sprayed).
Test method: observe and touch to check if there is sticky touch.
Check quantity: check every floor according to the number of two, but not less than 8.
3. Allowable deviation items
The allowable deviation of the installation of the extruded plate shall comply with the provisions of the following table.
Allowable deviation and inspection method for installation of extruded board
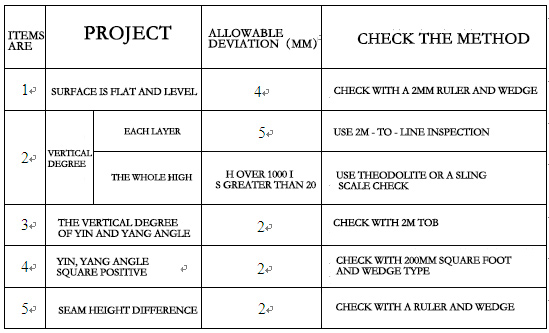
Allowable deviation and checking method of insulating mortar
Six, other matters needing attention
1., the construction of all types of professional work should be closely coordinated, reasonable arrangements for the process, is strictly prohibited reverse process operations.
2. to wipe the polymer mortar insulation wall should not be arbitrarily cut holes, such as do, should meet the design strength of wall protection layer shall be installed, pay attention to the surrounding objects should be restored immediately repair.
3. kinds of materials should be classified storage and listing marked material name to avoid misuse.
4. summer construction, should be appropriate arrangements for work time, as far as possible to avoid the sun exposure period.
5. rainy season construction, there should be rainproof measures, otherwise, may not carry out thermal insulation construction.
6., mixing polymer mortar, it is advisable to use an electric mixer, clean with bi.
Seven, finished product protection measures
1., strengthen the education of finished product protection, improve the awareness of the finished product protection of construction personnel, and implement the regulations on the protection of finished products
2., the construction of all types of professional work in close coordination, reasonable arrangements for the process, strictly reverse the process operation
3. of the finished insulation wall, not free to dig holes, especially the wall bracket must be buried in advance bownpipe.
4. do not put flammable and solvent chemicals on the Extrusion board, and do not do electrical welding on it
5, should prevent heavy objects hit the wall, such as the removal of scaffolding, strictly prohibit the use of the window as scaffolding fulcrum or fixed point, to prevent damage to hit. Doors and windows to prevent displacement deformation, plastering, pay attention to the windows and doors do not pollute the surface.
Eight. Safety assurance measures:
1, operators must pass three levels of education before they can mount guard.
2, outside the work must set up protective railing.
3, in the outer shelf operation, such as in the same vertical layer operation, personnel should be up and down two layers stagger each other, cannot simultaneously in a vertical line operation.
4, handheld power tools must have good insulation performance.
5. No flammable or solvent chemicals shall be placed on the upper part of the Extrusion board. No electric welders work on the extruded board is strictly prohibited.
6, high-altitude work is strictly prohibited to throw down the scrap, the lower angle material should be placed in the cement bag, centralized handling downstairs.
7, is strictly prohibited with after work, not in the hands of the foot, slapstick laughter.